An Eye on… Fujifilm Wide Format
March 13, 2023 by Jack Gocher
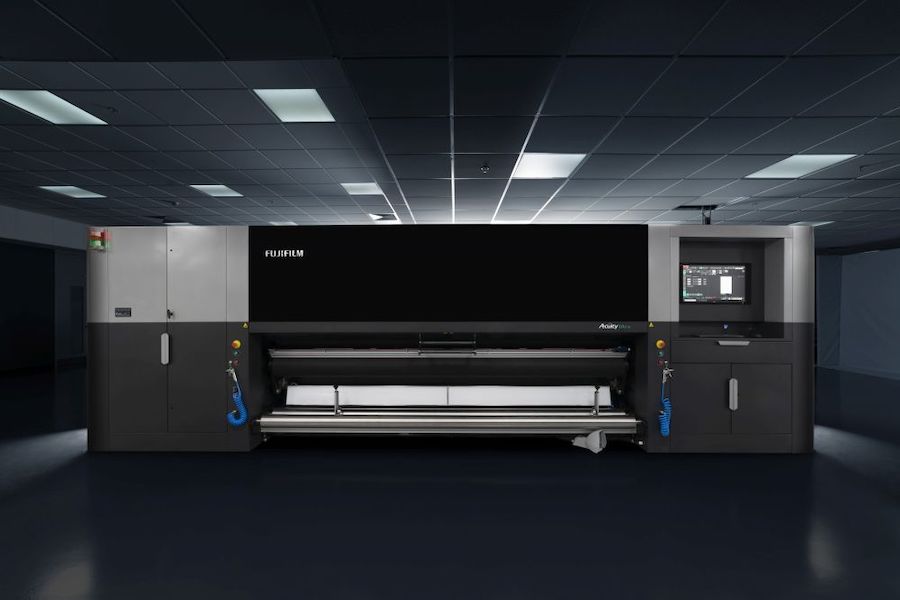
I recently visited the worldwide headquarters of Fujifilm’s Wide Format and Speciality Ink divisions in Broadstairs. Despite working in this industry for 26 years, Fujifilm was a company I didn’t know much about, and I wanted to put that right.
What I got was a masterclass in running a modern and efficient manufacturing and distribution site, with advanced Lean Manufacturing and Continuous Improvement processes and a visible commitment to improving sustainability across the entire operation.
Broadstairs in Kent seems an unlikely venue for such a prestigious global enterprise and one that certainly raises the eyebrows of overseas visitors as they enter the postcode into their sat nav. It was initially based there for sound business and economic reasons and is still at its original site because of the dedication, determination and commitment of the people working there.
During the 1940s, Alexander de Gelsey, a young man from Hungary, arrived in England for a new life. He wanted to be a chemist, first manufacturing ink in his bathtub. He soon identified the screen-printing market and created specialized inks for it. In the 50s, he teamed up with a manufacturer of screen-printing machinery to form Sericol and built the factory at its current site in 1961. After various acquisitions and accreditations, Sericol remained a market leader in screen printing ink manufacturing. But in the late 90s, one man within the company had a vision of where the market was heading that would shake the company to its core. That vision was digital printing – and he wasn’t wrong.
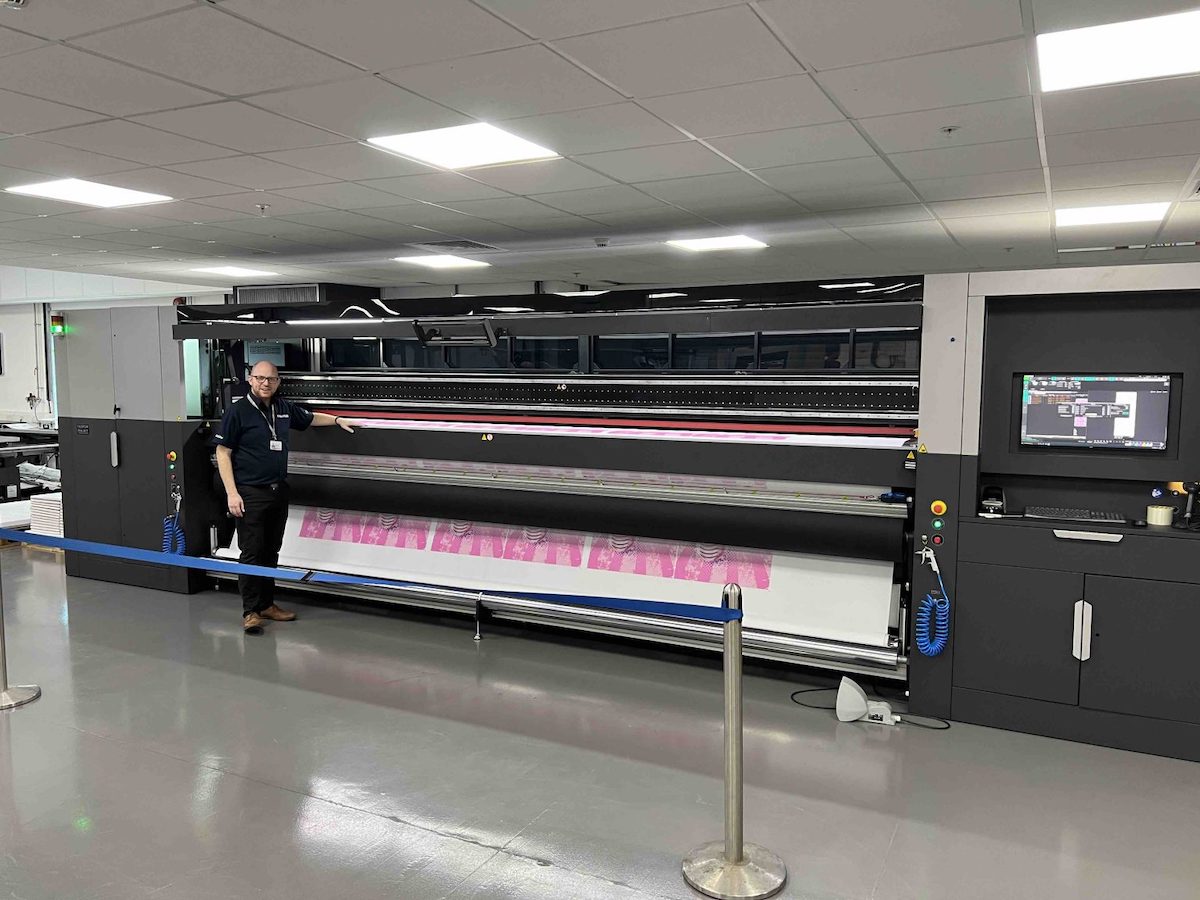
Kevin Jenner, Fujifilm Wide Format Systems’ European Marketing Manager, reveals the concerns this caused at the time, “This was a big deal for Sericol because screen printing had been a very successful and profitable business for many years. Also, there was a big difference in manufacturing ink that could go through a screen printer and ink that could pass through the tiny nozzles of a digital printhead. But it was the right thing to do and, in my view, showed how this company has remained successful over many decades by identifying and responding positively to the changing needs of the market and our customers.”
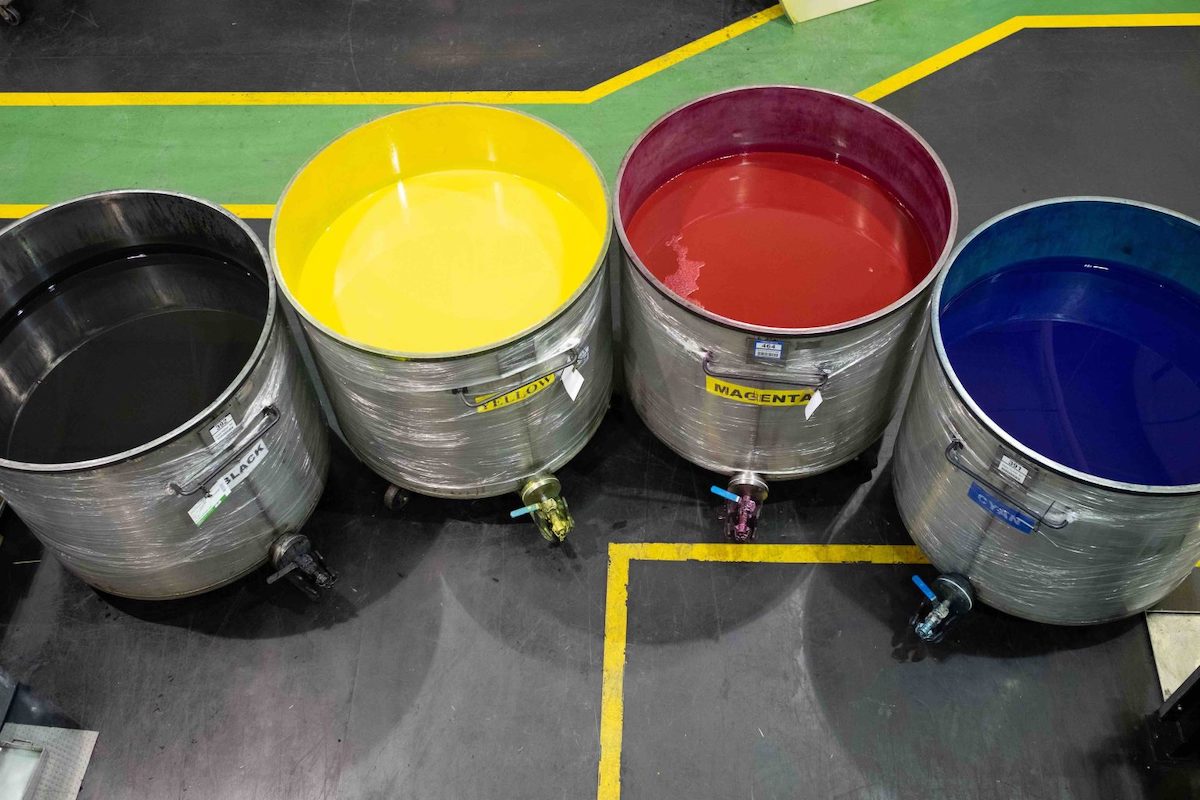
By 2005, UV inkjet ink manufacturing was very much in place, building a strong market and solid reputation. So much so that Sericol was acquired by the giant Fujifilm Corporation. It is a testament to the people of this company, many of whom have worked for the company since well before this acquisition, that despite the many pressures faced over the years, this manufacturing plant, situated somewhat out of the way on the East coast of Kent, is one of Fujifilm’s shining jewels.
Sustainability through actions, not words
Over the years, the Broadstairs site has won many awards, including Queen’s Awards for Environmental Achievement and Factory of the Year. Key to this success is their adoption of a program called Continuous Improvement.
Also underpinning everything that happens at this site is a true commitment to meeting the company’s sustainability goals. Kevin is keen to talk about this, “I always feel we are in a difficult situation in terms of communicating what we are doing around sustainability. Companies are making grand claims, but when you look under the bonnet, many are not doing as much as they would like you to believe. We have never wanted to be tarred with that brush, but we also want to let people know about some of the amazing things we are doing. We have built sustainability into all of our processes, with experienced, knowledgeable team members who are constantly looking at ways to reduce waste and energy and minimize the amount of new raw materials we use.”
On my visit to the site, I saw much of this for myself. I’m not an expert on designing and delivering measurable practices for improving sustainability, but it was evident that much thought, effort and investment was going into implementing tangible, results-oriented processes. There are already solar panels in use, and with further plans to install vertical wind turbines, Fujifilm is aiming to generate 20% of the site’s electricity requirements using renewable energy by the end of 2023.
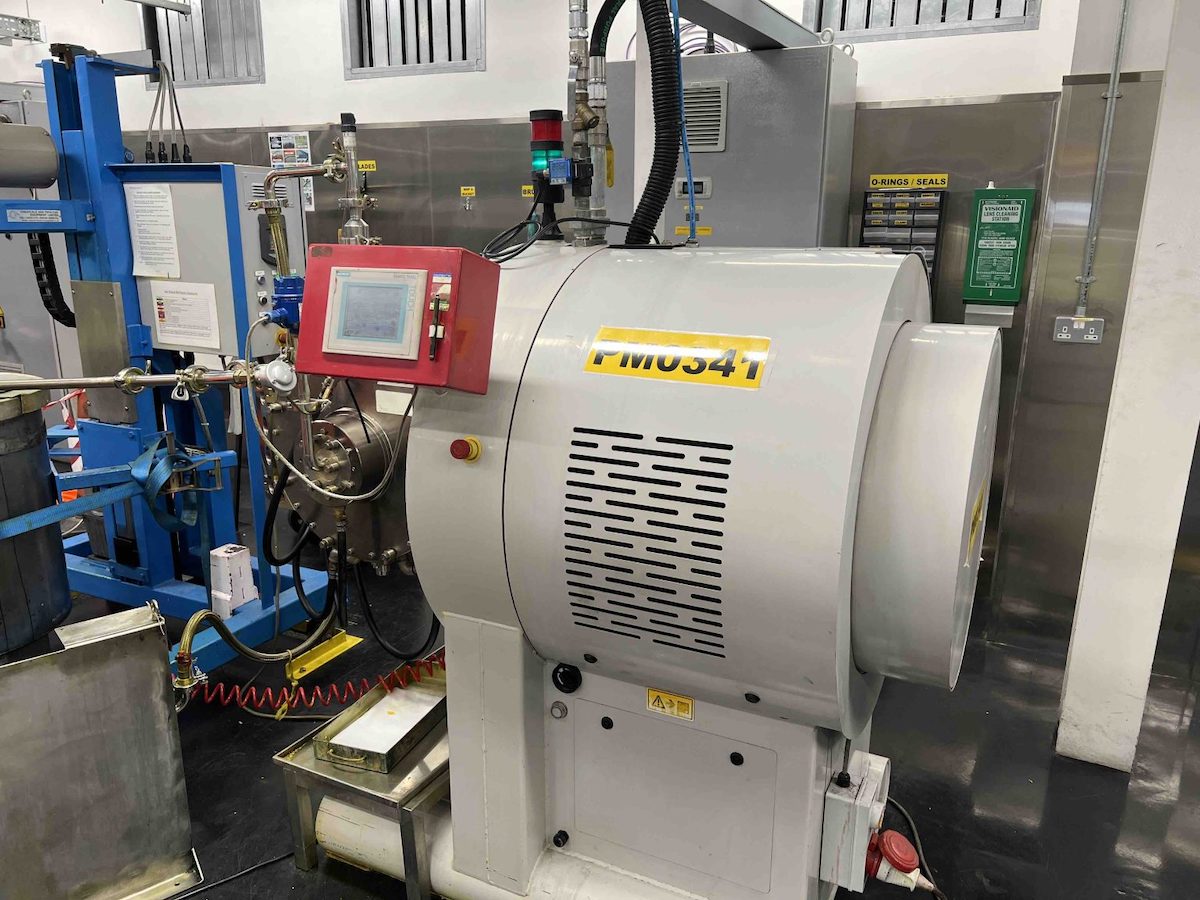
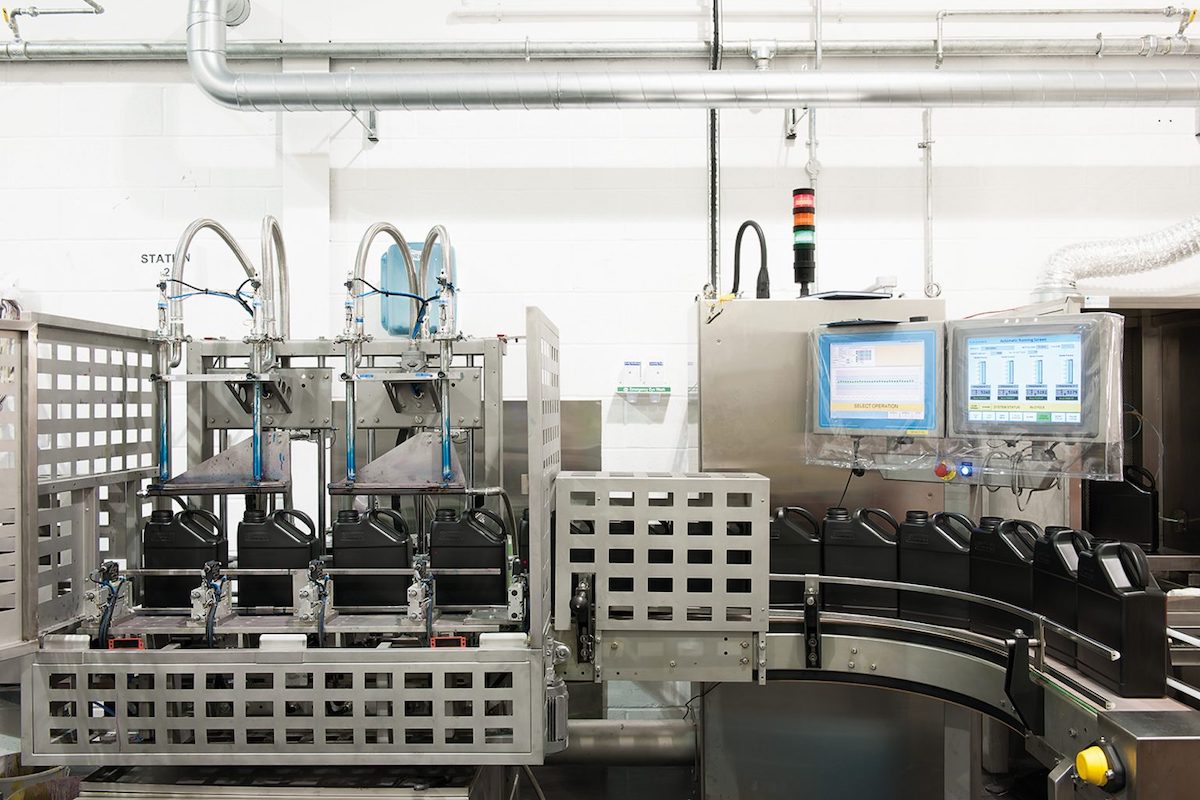
There were waste receptacles for everything and in all departments, including administration, R&D and the factory. I was assured that nothing has gone to landfill from this site for several years, and the Zero to Landfill formal accreditation is due to be awarded in 2023.
Continuous Improvement
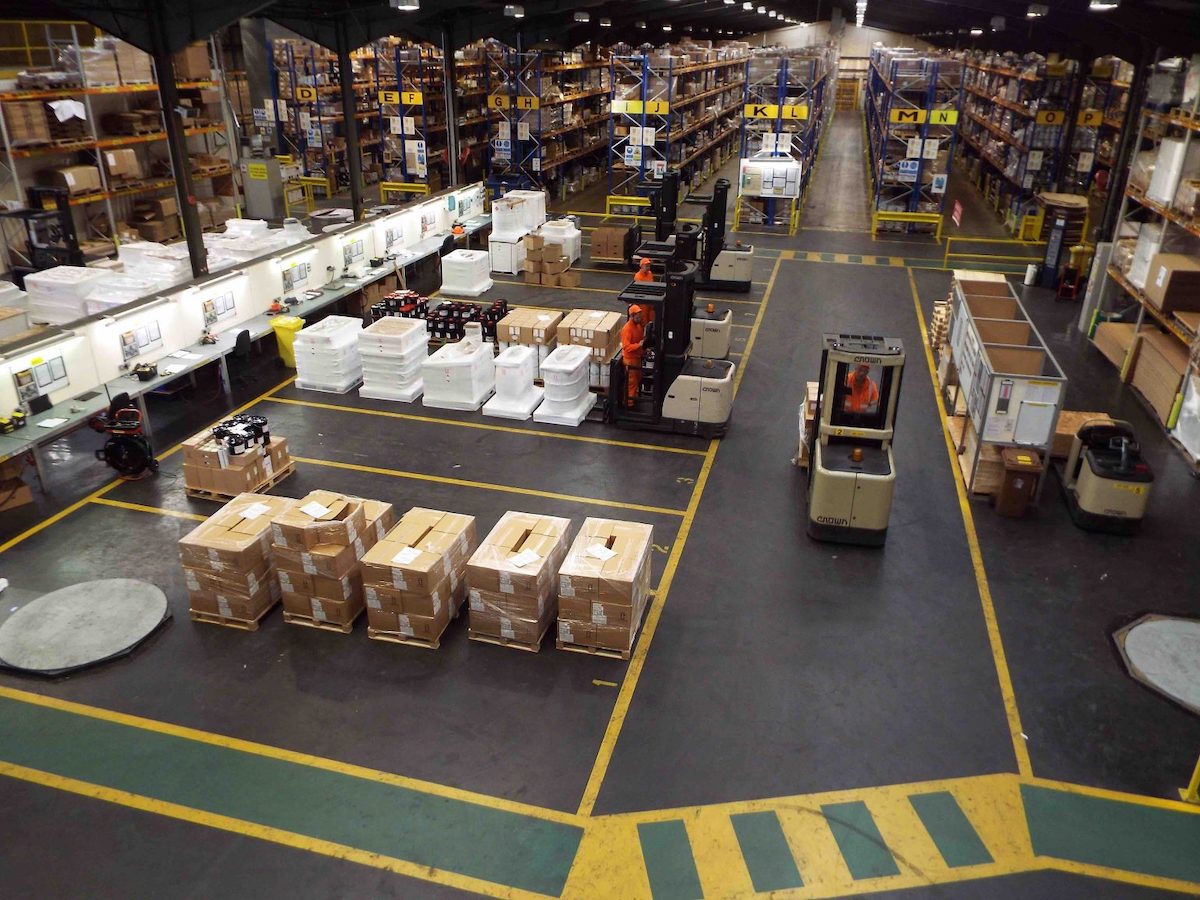
Another way to reduce waste is to get things right, so you don’t have to do them again. The factory has an outstanding 100% RFT – Right First Time in Digital Manufacturing and 97% in Analogue Manufacturing. “In 2005, when Fujifilm first took over, our score was just 45%,” says Gary Burgess, the site’s Manufacturing and Continuous Improvement Manager. “To achieve this transformation in customer satisfaction, we have taken everyone who works here on a journey with us to improve every aspect of our operations. It’s great to see it being recognised and successful.”
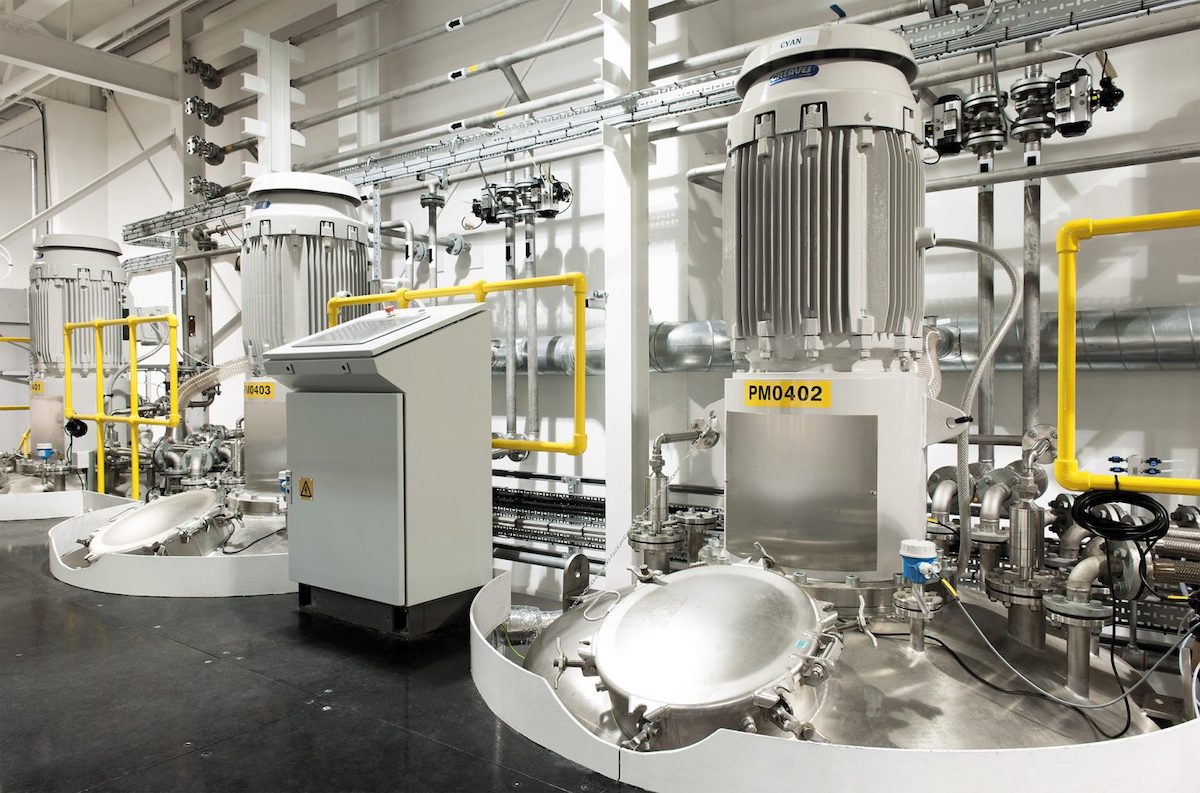
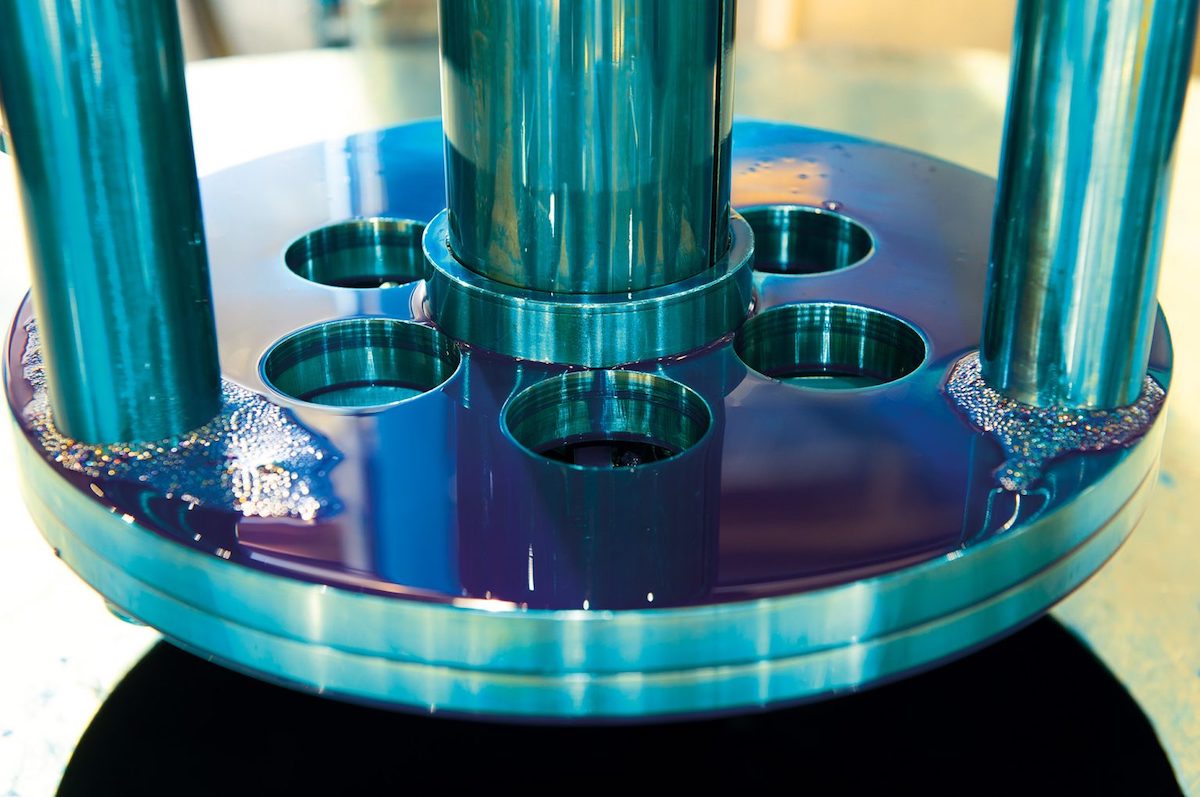
Communication is possibly the most important element of achieving positive results through Continuous Improvement. “If employees don’t know what is happening, we can’t expect them to support or replicate it,” says Gary, adding, “For example, one of our most popular ideas is the operators’ issues board where any ideas, constraint, wishes or concerns can be highlighted. Employees will get feedback to anything raised the following morning at their 5-minute morning meeting. Instant feedback lets the team know that anything raised by them is important to the management team and will get dealt with, ensuring we have an engaged and empowered team.”
Fujifilm places a considerable emphasis on creating a positive culture within the business. Continuous Improvement requires everyone to be involved in shaping and delivering it. “We have introduced proven techniques for visual communications in the workplace, such as Kamishibai and Electronic Process Control (Takt) Boards. “These are excellent tools for delivering great productivity and performance improvements. As a team, we have delivered them with consistency and determination. On top of that, we re-enforce our commitment to best practice so that we can achieve outstanding operational excellence.” adds Gary.
The Kamishibai boards are a lean manufacturing tool used to visualize data in manufacturing facilities and track the status of various activities happening across a production process. “This has been adopted with enthusiasm by our team leaders, operators and office staff because it provides a simple, visual task reminder. The boards are easy to set up and install and they ensure repetitive tasks are completed. This simple technique has made huge improvements to our efficiency and productivity,” Gary says.
To ensure the team is encouraged and supported to be part of the CI strategy, Gary highlights other important factors. “We ensured some quick wins to help the programme gain some early momentum. We also tried not to make too much of a big thing about it. People can be put off by big launches and meaningless jargon. We wanted everyone to see we were serious through actions, not words. We wanted to ensure we captured EVERY problem in the organization and saw each one as an opportunity to improve. This gives people more responsibility and is key to empowering them as part of the overall programme.”
Commitment to quality and improvement greatly extends to Fujifilm’s manufacturing and R&D work in the laboratories. Like in the factory and the offices, improvements have led to significant cost-savings and a more environmentally-friendly, sustainable workplace. The whole area is designed for efficiency and productivity, is spotlessly clean and organized and staffed by friendly, determined and clearly very hard-working people.
Don’t forget the printers
It is quite easy to get carried away by seeing all the great things happening in the laboratories and factory floors. But I was also interested to hear more about Fujifilm’s printer manufacturing. In 2019, the company returned to the drawing board to define what it called a ‘new blueprint for UV inkjet print performance’. The result was a brand-new range of Acuity printers that have already captured the market’s attention since their launch at FESPA earlier this year.
Seeing the testing and validation in action in Broadstairs, you can see the incredible attention to detail that goes into these machines. They are big, they are tough, they are fast, and they print some seriously good-looking output. They also manage to do this at a competitive price!
Kevin explains, “When it comes to printers, customers look at three key elements. Speed, quality and price. Raising or lowering the bar with any of these elements will always affect the others. Our challenge is to minimize any compromise to deliver printers with the highest possible speed and quality at the most competitive price. I believe Fujifilm has done that with the Acuity range, and many in the market agree.”
To close
My visit to Fujifilm was eye-opening. This is a huge organization that is demonstrably focused on looking after its staff, its customers and the wider planet. I will follow their progress with interest, particularly the commitments to zero landfill, increasing renewable energy and minimizing the use of new raw materials. Many thanks to Kevin and the team at Fujifilm for welcoming me to the site and showing me around.
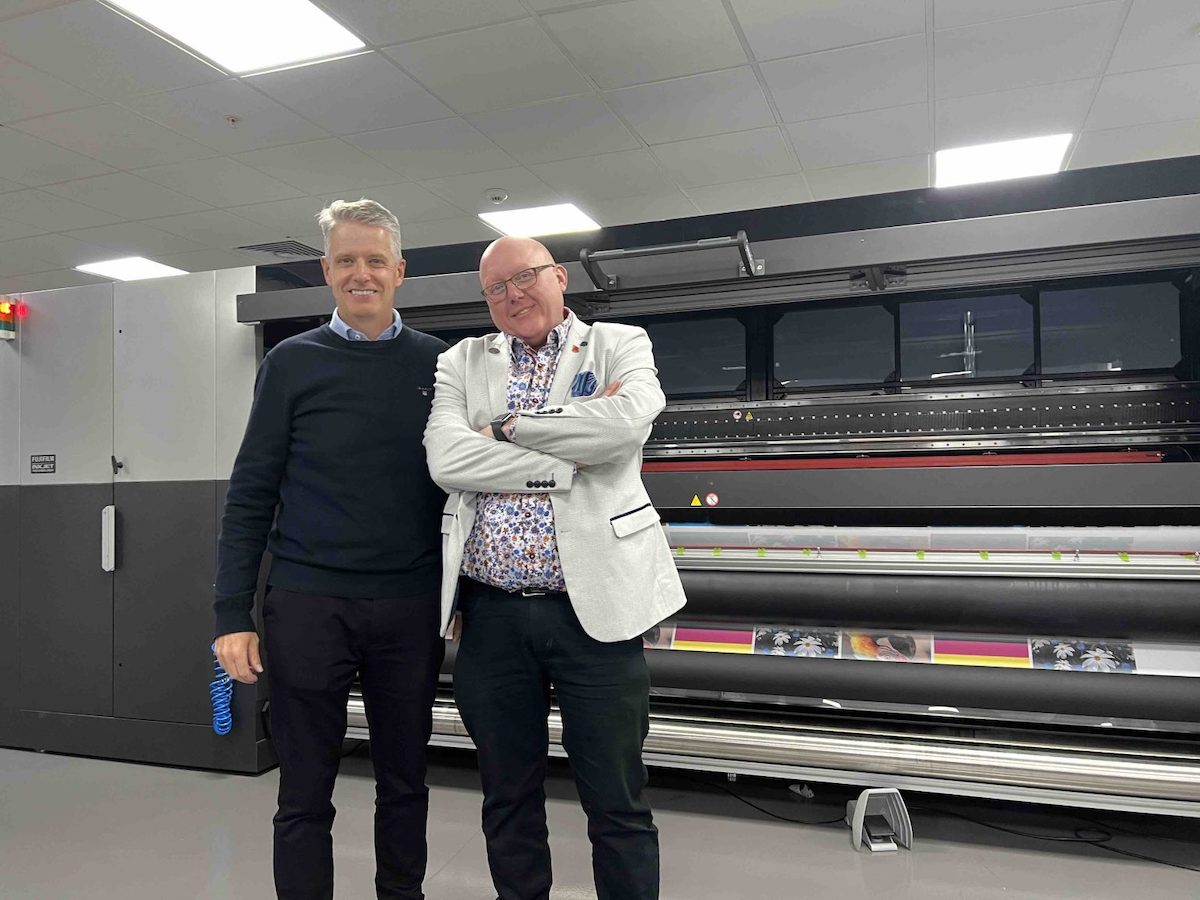
To find out more, visit their new website here.
Read more articles
The Most Important Checkbox in your RIP Color Management Settings
If you’re serious about color accuracy in your printshop, you’ve likely explored output profiles for your large format printers….
The Future of Large-Format Printing: AI, Sustainability, and Remote Innovation
This article was previously published on printvergence.com At HP we are already looking to the year ahead and all…
What are the complications of ICC RGB profiles?
As content creators, whether you’re a photographer, graphic designer, or digital artist, understanding the role of ICC RGB colour...