Can you coat it? Yes, Drytac can!
May 17, 2022 by Glen Fitzgerald
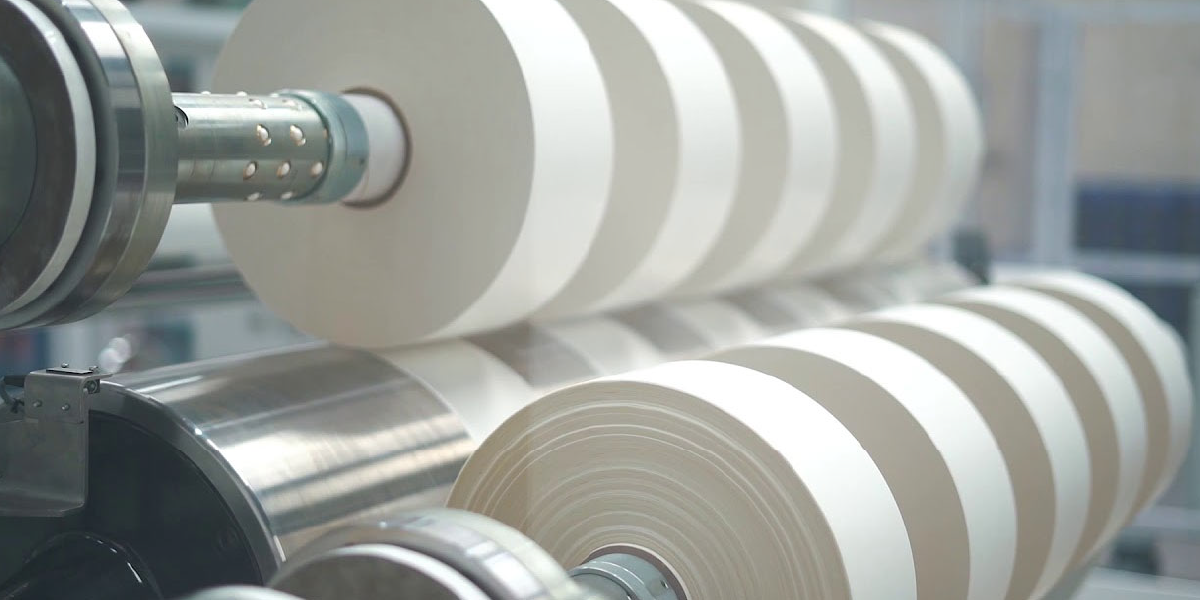
Selecting the right adhesive is critical for the success of many different types of applications and projects. Simply put, if you do not get this choice right, you risk the hard work you put in to creating the application, and potentially put the entire job and installation in jeopardy.
In my role at Drytac, it is my responsibility to grow the custom coating side of the business and our existing product offering. This covers both signage and print applications, as well as a range of key manufacturing industries such as medical, renewable energy and transportation, where Drytac is challenged to provide the right adhesive for all kinds of projects.
A big part of my focus is introducing industrial tape converters to Drytac as a partner to help fabricate PSA components that are an integral component of a manufacturer’s final product. The adhesive choice is very much an important part of this process.
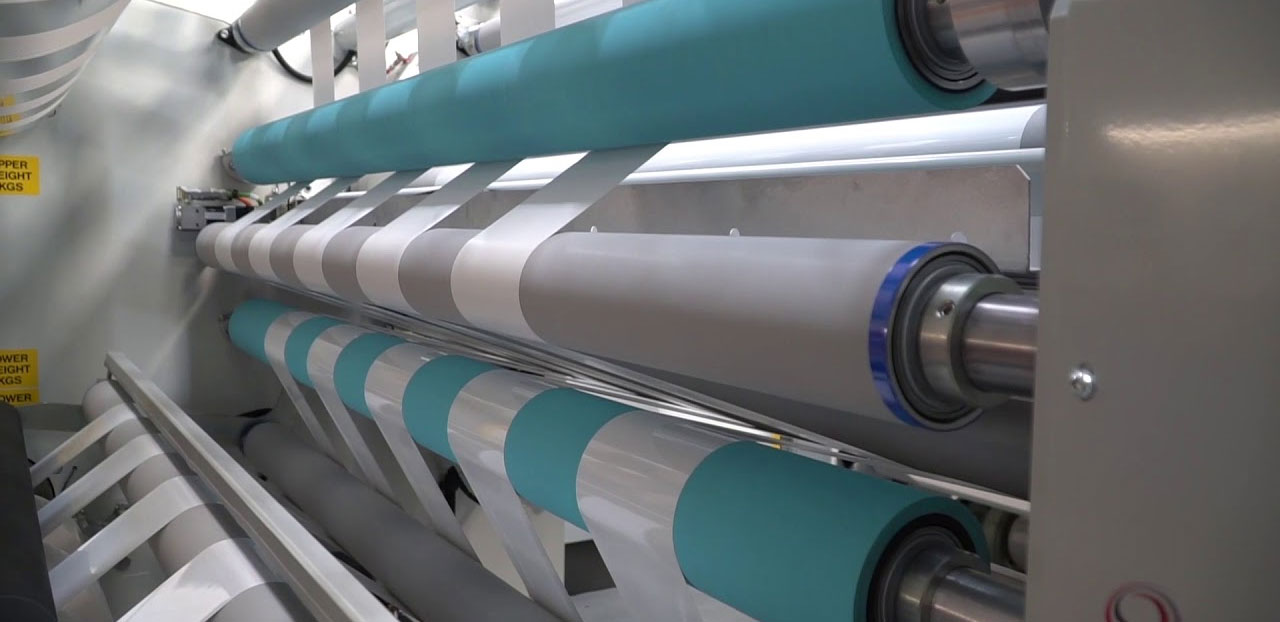
Initial tack or wet grab, shear strength, optical clarity, colour, permanent or removable characteristics, temperature and solvent resistance all need to be considered when designing a custom tape or adhesive to a specific customer application. If the wrong adhesive is chosen, it can lead to product failures which can damage the reputation of our customer’s final product.
With that in mind, what should companies look out for when selecting adhesive materials for work? First and foremost, you need to consider the quality of the product you will be working with and the reputation of the manufacturer that supplied the material. As is the case with all kinds of material, you get what you pay for, and opting for cheaper, less-known brands can be a bit of a risk.
Next, do some research into the type of technical support you will get from the tape manufacturer. Not only is the adhesive choice important for the final product, but the other components play just as significant a role. The adhesive carrier and release liner, if required, are critical for the overall performance of the tape throughout the manufacturing process, from coating the material, to the converting or fabrication of the product to the final use of the tape in the manufactured component.
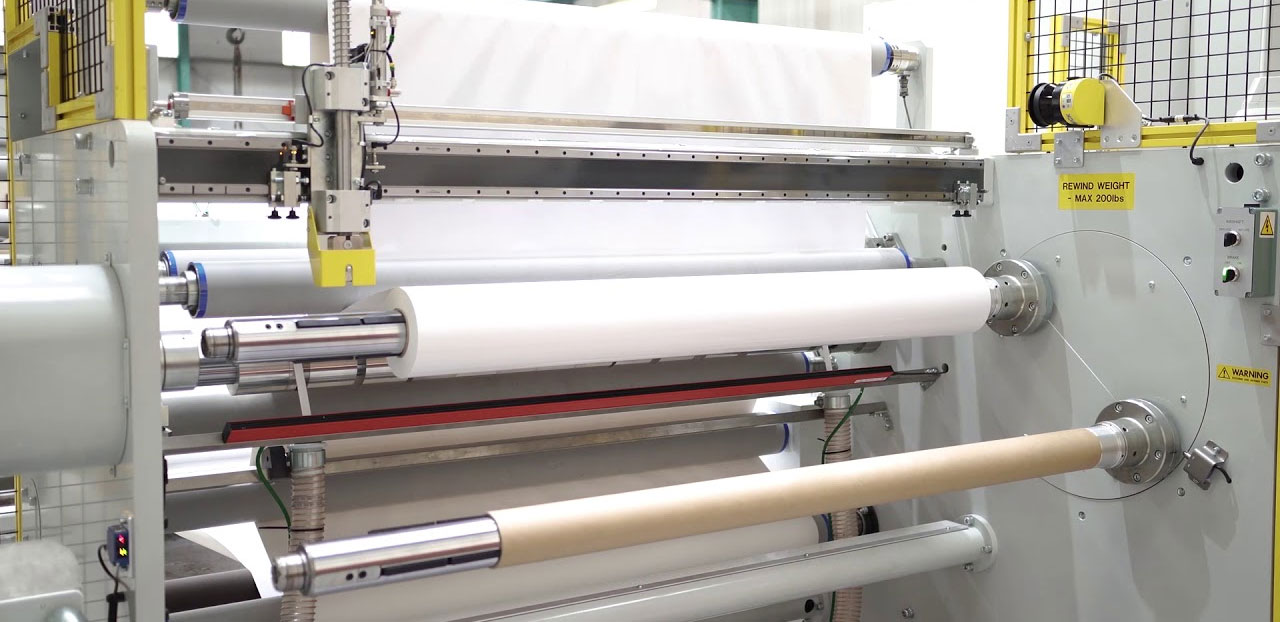
Finally, consider the level of post-sales customer support you are likely to receive from the tape manufacturer. Once the tape is produced and sold, customers need the proper level of support to ensure that they receive their product on time every time. It is for these reasons that Drytac is extremely well placed to help customers from a wide range of markets with their adhesives queries, no matter what base materials they are working with.
The Drytac team can help with customers’ most challenging applications or ideas by serving as a design consultant and sounding board throughout the product development process. The technical sales and engineering teams can assist with proper material selection, functional prototypes and working with our tape converting partners to bring your product ideas to market.
We have plenty of examples of how by working with customers, they have been able to use Drytac's new adhesive products across areas such as renewable energy, PSA labels, point of purchase display, military, and wallcoverings. The knowledgeable and experienced Drytac team, working out of our manufacturing facilities in North America and UK, help to establish a global footprint for your ideas
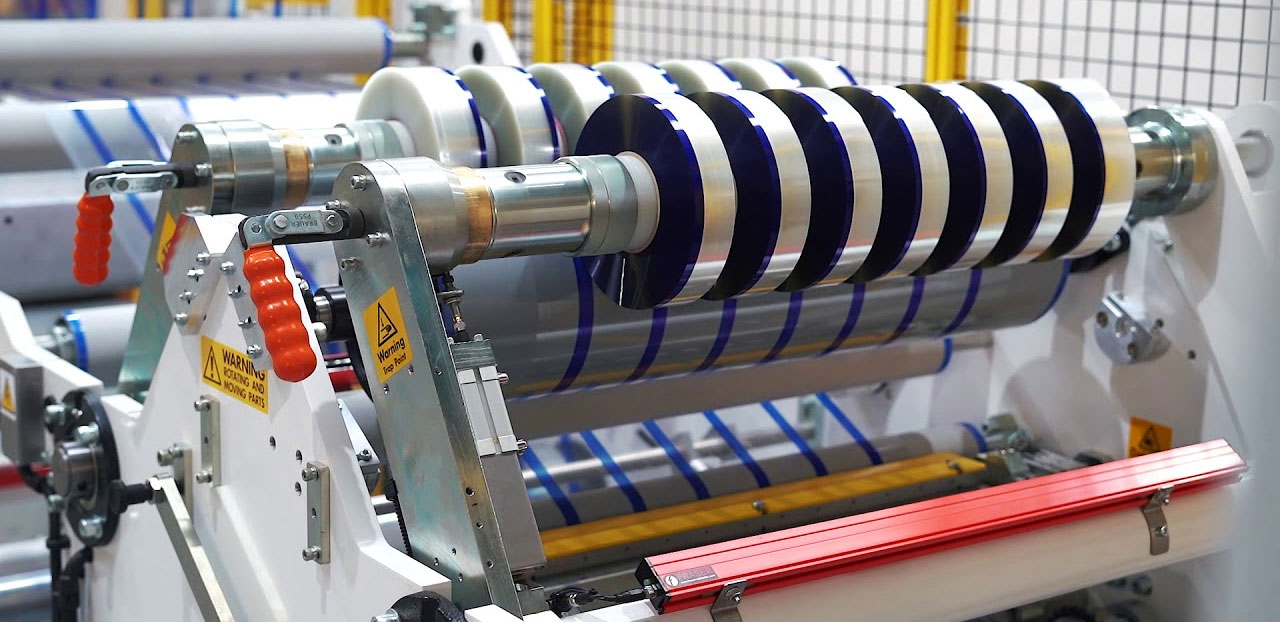
So, as you can see, Drytac is a very capable company that can provide top quality print material, as well as custom coating and adhesive solutions. And as always, if you are using Drytac material in your print workflow, remember to download the correct ICC profile using the ColorBase Profile Search tool to ensure optimal efficiency and color management.
Read more articles
The Most Important Checkbox in your RIP Color Management Settings
If you’re serious about color accuracy in your printshop, you’ve likely explored output profiles for your large format printers….
The Future of Large-Format Printing: AI, Sustainability, and Remote Innovation
This article was previously published on printvergence.com At HP we are already looking to the year ahead and all…
What are the complications of ICC RGB profiles?
As content creators, whether you’re a photographer, graphic designer, or digital artist, understanding the role of ICC RGB colour...