The Process Control Cycle: How To Maintain Consistent and Predictable Color Quality
July 8, 2024 by Shelby Sapusek
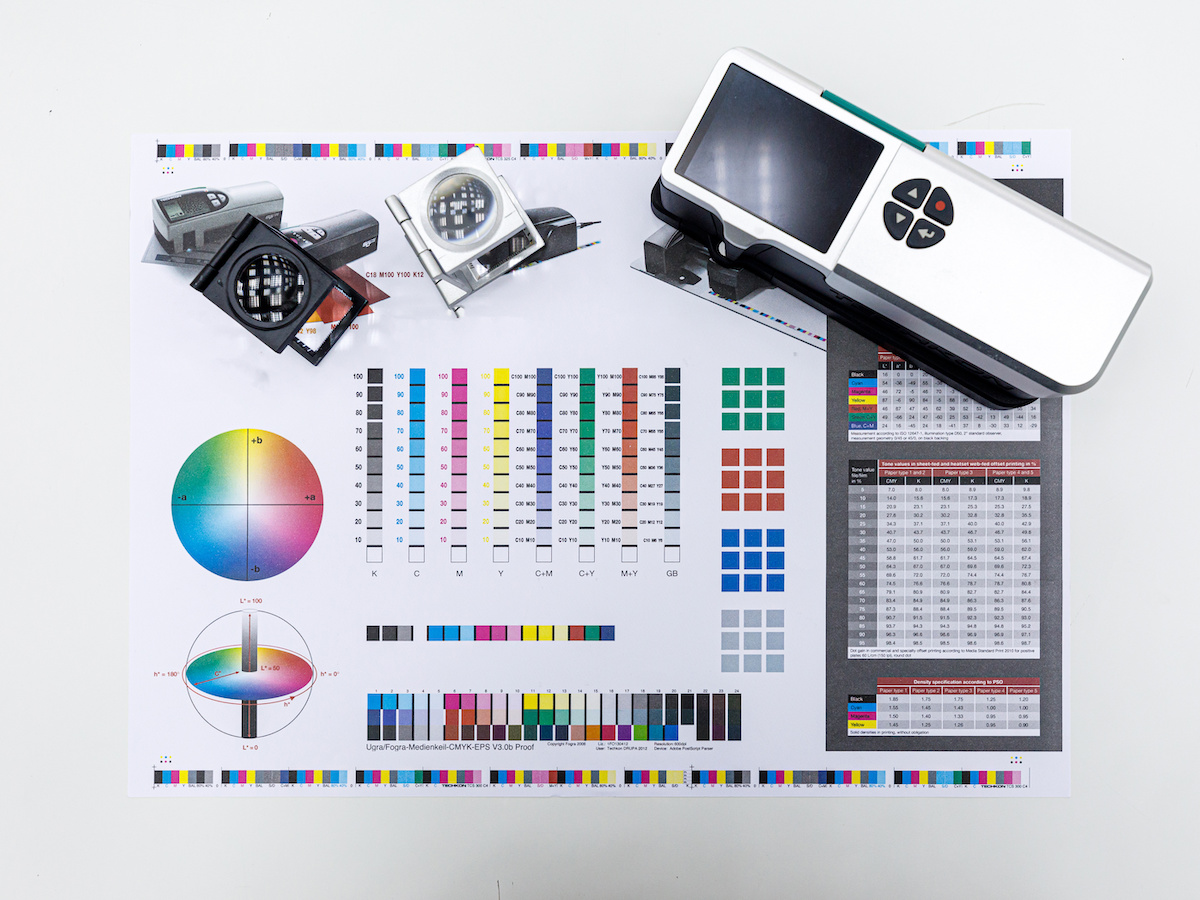
One of the best ways to achieve consistent and predictable color quality on a printer is to calibrate it and create a custom ICC profile for it. But the work doesn’t stop there. To maintain consistent and predictable color quality, you need a verifiable color management strategy that centers around process control.
When you choose to implement process control into your color management strategy, you will ultimately save yourself money in ink and media as well as save time by not having to repeat jobs.
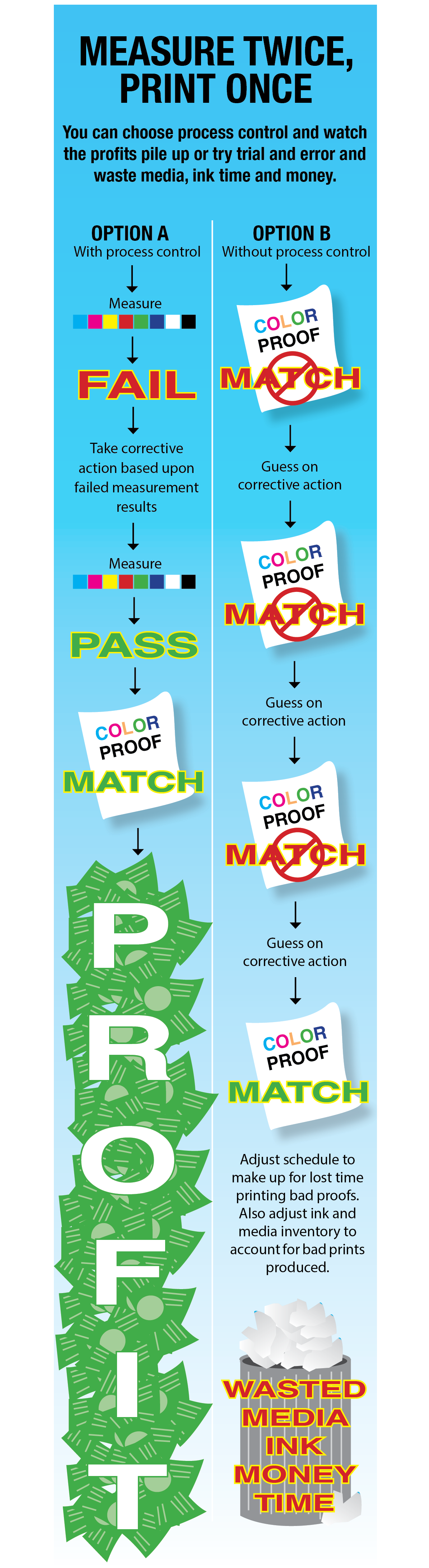
Process Control Is Cyclical
Printer profiles must be maintained; in much the same way that a car does.
When you buy a vehicle, at some point you need to take it in for maintenance which often includes an oil change. Once the oil has been changed, the maintenance provider will often place sticker on your windshield as a reminder of when the next service is due.
That’s because the maintenance needs to be ongoing. If the car only gets one oil change and it’s never checked again, its engine will eventually seize up and fail. Through everyday wear and tear, the amount of oil will decrease and parts will begin to deteriorate.
The same is true for a printer profile. Like a car, a printer is a machine that is in constant operation and will experience wear and tear over time. That can affect a profile’s performance; which is why the printer must be maintained and profile verified.
The Color Management Pyramid’s Role In Process Control
As a certified instructor for PRINTING United Alliance’s and Idealliance’s iLearning+ color management program, I often refer to the Color Management Pyramid as a guide on how to build a custom ICC profile. The pyramid is based on agreed upon industry best practices for color management.
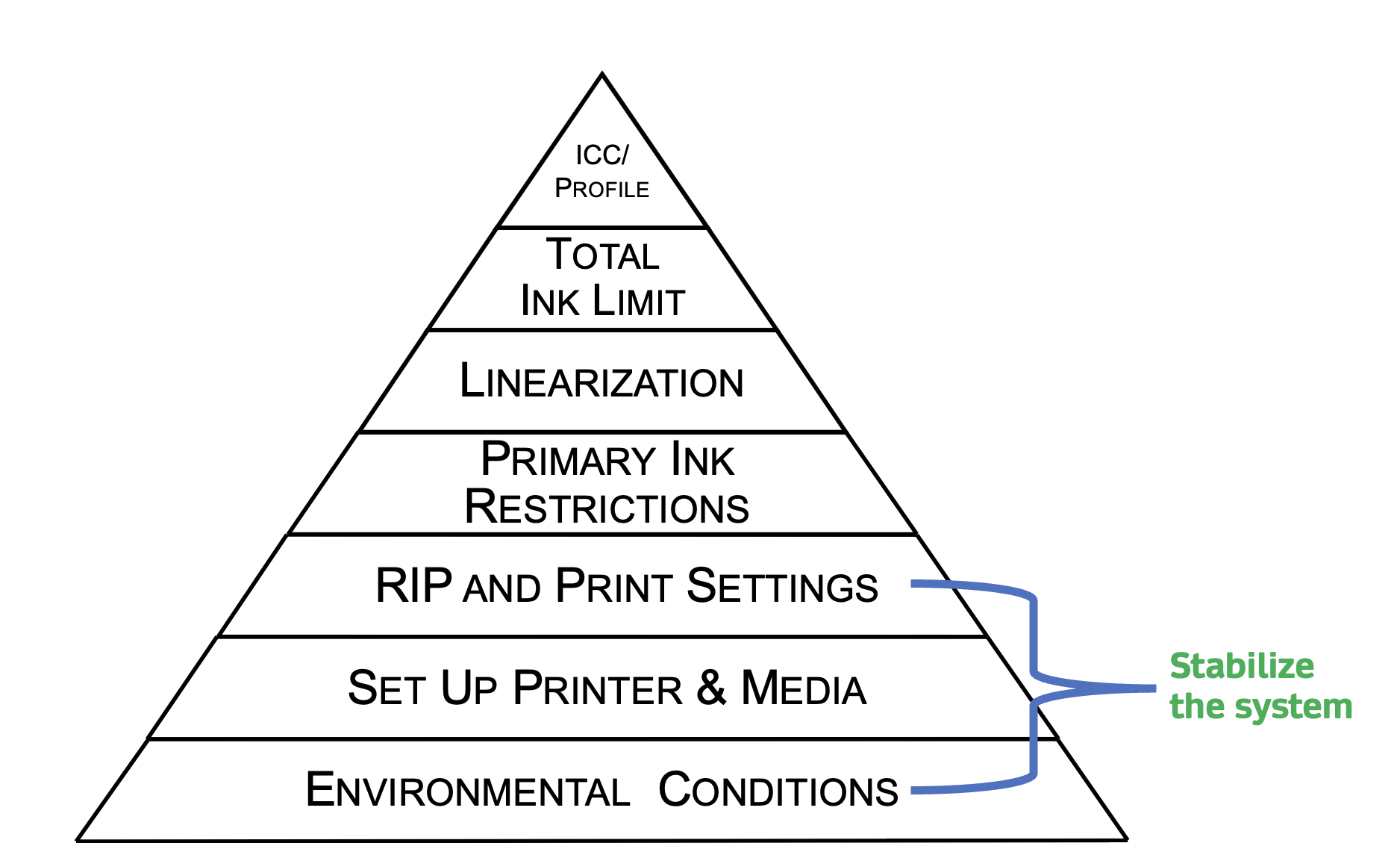
To use it, you start at the bottom of the pyramid and work your way up. The first three levels of the Color Management Pyramid are important elements of process control. We refer to it as stabilizing the system.
- The Environment: If you refer to the pyramid image, the first consideration is the environmental condition in the printing space. You want to make sure your printer has clean power and is absent of dust and dirt. Temperature and humidity should also be monitored carefully. The optimum temperature in your printing environment should be around 70 degrees Fahrenheit and the relative humidity should be non-condensing and around 50%.
- The Printer and Media Settings: You’ll want to ensure that the settings are correct for the print head height and alignment as well as your media feed and UV heat lamp settings if applicable. Don’t forget to perform a nozzle check daily too. It’s one of the easiest and most important checks you can make on your printer.
- The RIP and Print Settings: These settings refer to the preferred options in your RIP software and on your printer. They include resolution, pass count, variable dot settings, etc. Understanding and applying the optimal settings for your RIPs and printers will help you set up your system for success.
Once your system is stabilized, you can follow the steps in the rest of the Color Management Pyramid to create a custom ICC profile (which will be explained in a future article). A custom ICC profile serves as a baseline that describes a printer’s known good print condition at a specific point in time. But, as explained before, it must be verified frequently because it can be affected by changes in variables in the color management process.
Verification for Process Control
There are many variables that can affect a profile of a printer. They include replacement of printer parts, changes to inks or substrates and the environmental variances (temperature or humidity) as a whole. Therefore, it’s important to frequently verify your custom ICC profile to make sure it’s still performing at your preferred baseline.
To verify a profile, you need a spectrophotometer that is supported by a piece of software that can collect and analyze spectral data. You also need to choose a control target to measure against. This target should be a specific guideline such as GRACoL®. You can find free downloads of control wedges to download and measure on the Idealliance website.
Once you choose a target, you can print it out with the ICC profile applied. Measure the target into the software program and choose the guideline to measure against. In most programs, you can view the results numerically and pictorially.
The software will show you the Delta E number for each swatch of color on the control strip compared to the guideline so that you can see the mathematical difference between the swatches. These numbers and visual charts will help you determine whether your custom ICC profile is still performing as expected or if it’s time to re-calibrate your printer.
Keep The Cycle Going
Whether you have to re-calibrate or not, you need to frequently check up on your printer and profile. Ongoing maintenance of process control is necessary to maintain consistent and predictable color quality.
It’s a good idea to make one person responsible for verifying a printer’s performance over time. Having a strict routine where someone is logging results with time and date stamps will ensure that the necessary steps are taken to keep your printer performing at its best.
Read more articles
The Most Important Checkbox in your RIP Color Management Settings
If you’re serious about color accuracy in your printshop, you’ve likely explored output profiles for your large format printers….
The Future of Large-Format Printing: AI, Sustainability, and Remote Innovation
This article was previously published on printvergence.com At HP we are already looking to the year ahead and all…
What are the complications of ICC RGB profiles?
As content creators, whether you’re a photographer, graphic designer, or digital artist, understanding the role of ICC RGB colour...